Building a cubic-kilometer telescope at the South Pole seemed a chimera even for some of those involved in the project. But AMANDA had proven that if such a detector were built, it would allow great science to come.
The goal was simple in words but seemingly impossible in practice: 86 boreholes, each 60 cm in diameter and 2,500 m deep, had to be drilled and instrumented in seven austral summer seasons. Safety was a must, fuel needed to be used cautiously and the South Pole environment was just unavoidable.
And yet, IceCube was completed in the seventh construction season. By that time, at the end of 2010, the IceCube drilling team had beaten all records: less time and fuel per borehole, optimized hole shapes with almost perfect vertical alignment over the 2.5-km depth, and only a few safety-related issues. How was this possible? Blame the talent, expertise and strong will of a great team.

Four years after IceCube’s completion and with new projects and drilling seasons on the horizon, the team that led this feat has explained the details of IceCube drilling in two papers published today in the journal Annals of Glaciology.
“Although there was a lot of experience from AMANDA drilling, drilling for IceCube was a whole new ballgame. We continued learning lessons about the equipment and our techniques to the bitter end, but by the final seasons the drill and its crew were a well-oiled machine,” explains Terry Benson, a drill engineer at the Physical Sciences Laboratory (PSL), who started working on the IceCube drill as a young student and was one of the drill leaders during the last two construction seasons.
“It would have been impossible to build IceCube without PSL. With them, we overcame every challenge and the results were impressive,” says Prof. Albrecht Karle, the IceCube associate director for Science and Instrumentation.
Drilling to depths that almost reach the Antarctic bedrock also meant a larger diameter for the holes, since water starts to freeze immediately. And working at the South Pole meant that logistics and resources had to be extremely well planned and economized.
“It was important to conserve the expensive fuel so we wanted to avoid overdrilling the holes. However, if a hole was made slightly too small, so that a string got stuck, both the hole and the string of instrumentation could be be lost. This would have been a very expensive mistake. It was extremely important to have a good understanding of hole size and freeze back rate,” explains Lee Greenler, a mechanical engineer also at PSL, who led the team developing the heat transfer calculations that allowed the optimization of the drilling process.
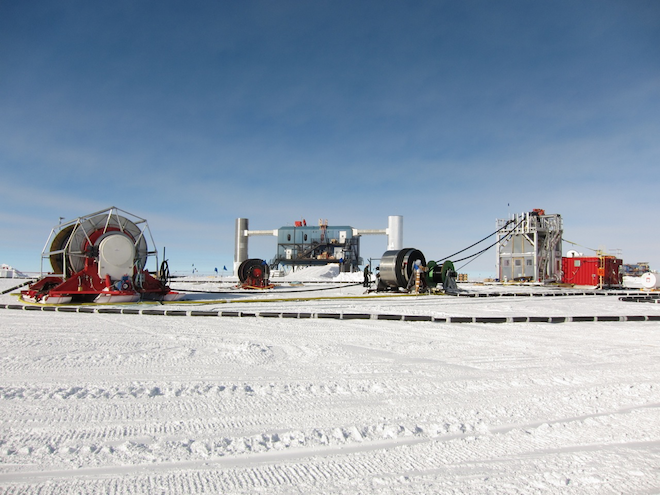
The drilling process started with four weeks of preparation and a crew of about 30 people. The seasonal equipment site (SES), which provided electricity and a stable supply of hot pressurized water, and the tower operations site (TOS) had to be excavated and commissioned. The SES remained stationary throughout each drill season, while drilling towers moved from one hole to another.
“We were drilling around-the-clock, with three 9-hours shifts and only Sundays off. In season 2009-2010, when we drilled 20 holes, we sent 88 people to the Pole, but also over 450,000 liters of fuel and almost 300 tons of cargo,” explains Jim Haugen, an instrumentation engineering manager at WIPAC, who has been leading the logistics of the IceCube polar seasons since construction began.
Drilling an IceCube hole meant shooting hot water at 80ºC through an instrumented drill head at the end of a continuous hose of about 2,500 meters. Then, during the ream phase, the drill was raised while the hot water continued to flow, enlarging the hole and keeping non-frozen water in contact with the hole walls so that it took longer to freeze back. Once 60 IceCube sensors (DOMs) were deployed, the hole completely froze around them over the following week or so.
An independent firn drill was used for the first 50 meters, since this first layer of lower density snow does not hold water. This improved system, designed after the first seasons proved the old firn drill to be very slow, allowed an increase from 13 to 18 or more holes drilled per season.
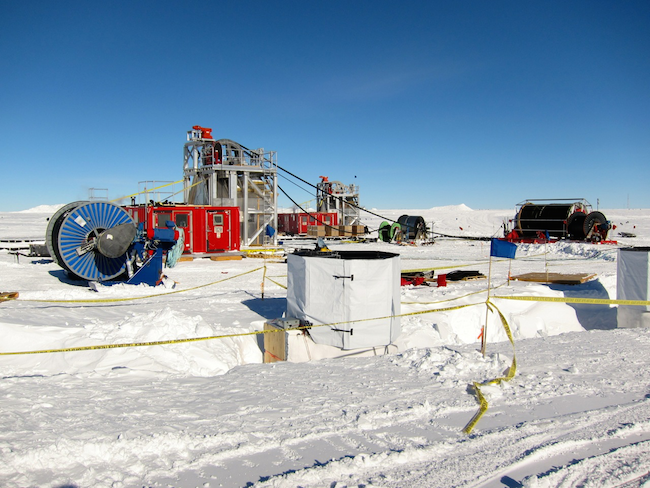
To drill IceCube was not an easy job, but the results now presented in these two papers show that it is possible to do large-scale production ice drilling in the Antarctic environment in a safe, efficient and predictable way. Dynamic engineering techniques based on year-to-year lessons learned and on retention of experienced crew members were critical in turning a chimera into the successful IceCube Neutrino Observatory.
+ Info “IceCube Enhanced Hot Water Drill functional description,” T. Benson, J. Cherwinka, M. Duvernois, A. Elcheikh, F. Feyzi, L. Greenler, J. Haugen, A. Karle, M. Mulligan, R. Paulos. Annals of Glaciology 55(68) (2014) 105-114. doi:10.3189/2014AoG68A032.
“Modeling hole size, lifetime and fuel consumption in hot-water ice drilling,” L. Greenler, T. Benson, J. Cherwinka, A. Elcheikh, F. Feyzi, A. Karle, R. Paulos. Annals of Glaciology 55(68) (2014) 115-123. doi:10.3189/2014AoG68A033.